3 Simple Techniques For Alcast Company
3 Simple Techniques For Alcast Company
Blog Article
The Alcast Company Statements
Table of ContentsSome Known Incorrect Statements About Alcast Company Some Of Alcast CompanyAlcast Company Things To Know Before You Get ThisAlcast Company Fundamentals ExplainedMore About Alcast CompanyAlcast Company - Truths
Chemical Comparison of Cast Aluminum Alloys Silicon promotes castability by reducing the alloy's melting temperature and improving fluidity during casting. Furthermore, silicon contributes to the alloy's strength and put on resistance, making it valuable in applications where toughness is essential, such as vehicle components and engine elements.It likewise boosts the machinability of the alloy, making it easier to process right into completed items. In this method, iron contributes to the overall workability of aluminum alloys.
Manganese contributes to the strength of light weight aluminum alloys and enhances workability (Aluminum Castings). It is frequently used in wrought aluminum products like sheets, extrusions, and accounts. The visibility of manganese help in the alloy's formability and resistance to breaking throughout manufacture procedures. Magnesium is a lightweight component that gives stamina and influence resistance to aluminum alloys.
Alcast Company - Questions
It allows the production of light-weight elements with exceptional mechanical residential or commercial properties. Zinc boosts the castability of aluminum alloys and helps regulate the solidification process during casting. It boosts the alloy's strength and firmness. It is commonly found in applications where elaborate forms and great details are required, such as decorative spreadings and certain automobile parts.
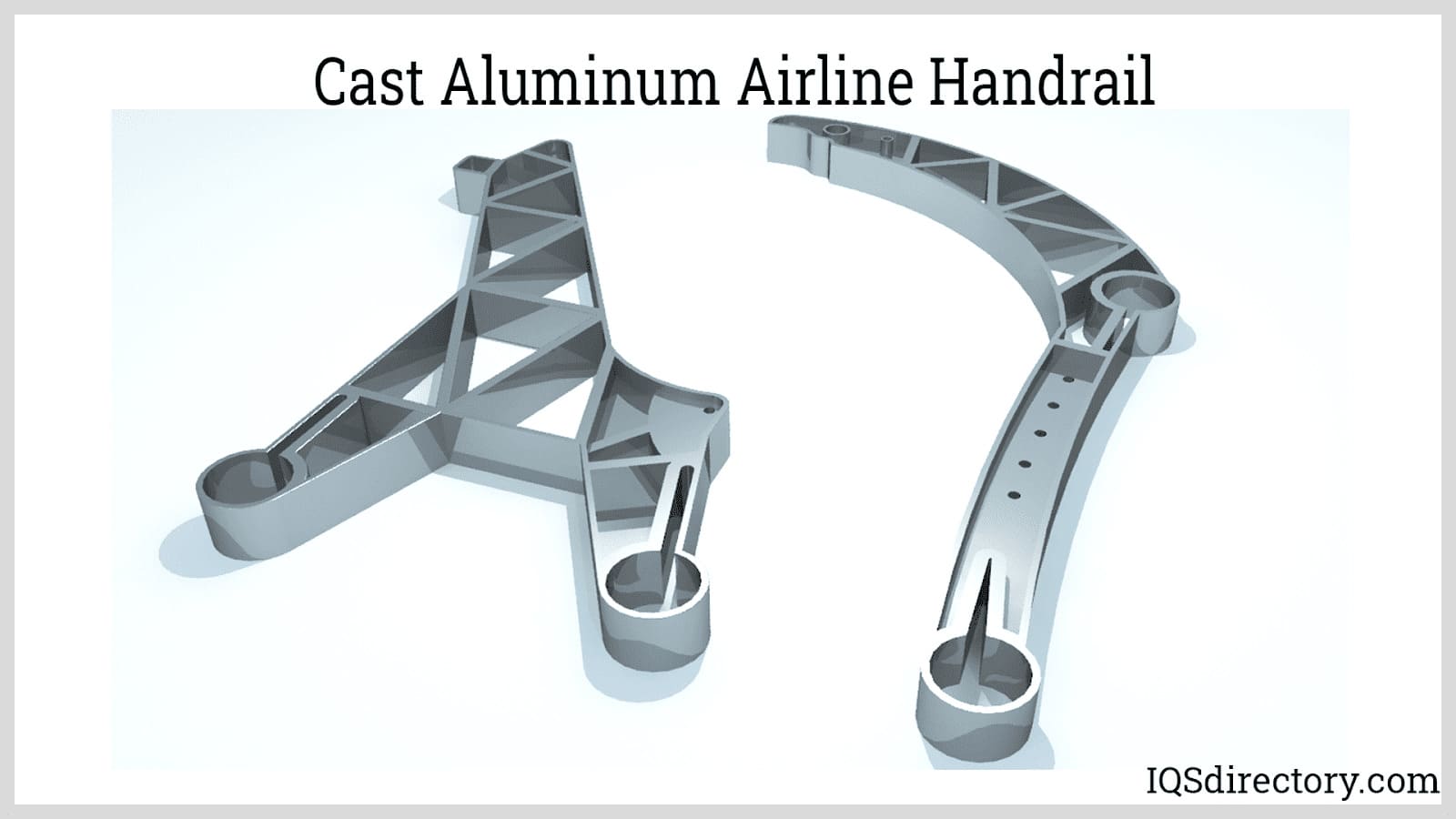
The key thermal conductivity, tensile strength, return strength, and prolongation vary. Select appropriate raw materials according to the efficiency of the target product created. Among the above alloys, A356 has the greatest thermal conductivity, and A380 and ADC12 have the most affordable. The tensile restriction is the contrary. A360 has the most effective yield strength and the greatest elongation rate.
The Only Guide to Alcast Company
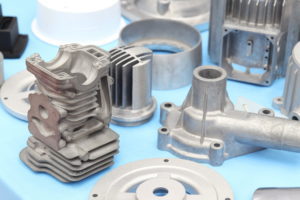
In accuracy casting, 6063 is fit for applications where detailed geometries and premium surface area finishes are critical. Instances consist of telecommunication units, where the alloy's exceptional formability enables sleek and cosmetically pleasing designs while preserving architectural integrity. In a similar way, in the Lighting Solutions sector, precision-cast 6063 elements create elegant and reliable lighting fixtures that need detailed forms and excellent thermal performance.
The A360 displays remarkable elongation, making it excellent for complicated and thin-walled elements. In precision spreading applications, A360 is well-suited for sectors such as Customer Electronics, Telecommunication, and Power Devices.
The Best Guide To Alcast Company
Its unique residential or commercial properties make A360 a beneficial option for precision spreading in these sectors, enhancing item longevity and quality. Light weight aluminum alloy 380, or A380, is a commonly used casting alloy with several unique features. It provides outstanding castability, making it an ideal selection for accuracy casting. A380 shows excellent fluidness when molten, guaranteeing detailed and detailed mold and mildews are precisely recreated.
In accuracy casting, aluminum 413 radiates in the Consumer Electronics and Power Tools sectors. This alloy's exceptional deterioration click site resistance makes it an excellent choice for outdoor applications, making sure durable, long lasting products in the pointed out industries.
The Alcast Company Statements
The light weight aluminum alloy you choose will considerably affect both the spreading procedure and the residential properties of the final item. Because of this, you must make your choice thoroughly and take an enlightened method.
Determining the most suitable aluminum alloy for your application will mean considering a broad variety of attributes. The very first classification addresses alloy attributes that impact the manufacturing procedure.
10 Simple Techniques For Alcast Company
The alloy you choose for die casting straight impacts numerous aspects of the spreading process, like just how easy the alloy is to deal with and if it is susceptible to casting defects. Warm breaking, additionally called solidification fracturing, is a normal die casting problem for light weight aluminum alloys that can lead to inner or surface-level rips or cracks.
Specific light weight aluminum alloys are extra susceptible to hot fracturing than others, and your selection should consider this. One more usual problem discovered in the die casting of aluminum is pass away soldering, which is when the actors adheres to the die wall surfaces and makes ejection hard. It can damage both the cast and the die, so you ought to look for alloys with high anti-soldering residential or commercial properties.
Rust resistance, which is currently a notable characteristic of light weight aluminum, can differ significantly from alloy to alloy and is an essential particular to take into consideration relying on the environmental problems your product will be subjected to (Aluminum Castings). Put on resistance is an additional building typically sought in aluminum products and can distinguish some alloys
Report this page